L'enveloppe doit
présenter plusieurs caractéristiques :
– La souplesse : elle
est repliée après chaque vol
–
La résistance : elle
doit supporter les contraintes mécaniques de pression exercés par le gaz
–
L'étanchéité : les
gaz plus léger que l'air ayant une molécule très petite par rapport à
l'air, il faut avoir une très bonne étanchéité pour pourvoir réaliser
des vols assez longs.
A
l'origine, divers matériaux furent utilisés :
–
La baudruche :
Membrane tirée de l'intestin du boeuf et du mouton
qui a surtout été utilisé en Angleterre.
Avec 8 couches de baudruche, ils arrivaient à
obtenir un poids de 213 gr/m² et une résistance de 1 200 kg par mètre
linéaire.
Avantages : très léger et très étanche (perte de
0,2 % par 24 heures)
Inconvénients : durabilité faible, coût élevé
–
Les étoffes :
On en trouve principalement deux : le coton et la
soie (rarement le lin)
Ils assurent la résistance mécanique, ils sont
ensuite enduits de caoutchouc ou de vernis pour assurer l'étanchéité.
Les différents cotons :
●
Le calicot : emploi
très courant, solide, pas cher mais lourd
●
Le percale : tissu
plus fin que le calicot, surtout employé sur les ballons civils
Les différentes soies :
●
La soie européenne,
les meilleures étaient italiennes et particulièrement française, appelé
taffetas, d'origine lyonnaise. Plus solide que la soie
chinoise et aussi plus régulière.
Son point faible est une grande altérabilité qui la
rendait inutilisable jusqu'à ce que les industriels ont réussi à
résoudre ce problème.
●
La soie chinoise
appelée soie ponghé ou ponghée, moins chères mais
performantes. Elle n'a pas ce problème d'altérabilité, elle est très
souple et prend bien le vernis.
●
Le tussah : c'était
rien d'autre que de la soie ponghée fabriquée en France à partir de soie
importée de Chine. Plus régulier que le ponghée chinois, il a été peu
utilisé car il prenait moins bien le vernis et était peu étanche.
A titre de comparaison, voici pour ces matériaux
une fois vernie et présentant une résistance de 1 000 kg/mètre linéaire,
le poids au mètre carré et le prix de l'époque (1910) :
–
Toile de
coton 400 gr
2 fr
–
Toile de
lin 300
gr 2 fr,50
–
Soie ponghé
200 gr 3 fr
–
Soie française
125 gr 10 fr
–
Les étoffes
vernies
C'est le moyen le plus ancien utilisé pour imperméabiliser les étoffes.
On enduisait les étoffes de vernis mais ce dernier devait avoir des
propriétés bien spécifiques :
–
séchage rapide
–
souple
–
doux
–
non poisseux
–
pas d'altération du
tissu
Les
vernis contiennent principalement deux sortes de substances :
●
L'une siccative
assurant l'étanchéité
●
L'autre émollientes
donnant à la composition le liant nécessaire et corrigeant les défauts
des éléments siccatifs.
Charles et Robert avaient employé un vernis à l'huile de lin cuite.
Conté mis au point un vernis très performant qui permettait a permit aux
ballons captifs militaires de la première république de tenir des mois
entiers sans ravitaillement en gaz.
Sa
composition précise et sa préparation se sont perdus mais voici les
principaux composants :
–
Huile le lin
siccative
–
Caoutchouc
–
Cire ou glu
–
Essence de
térébenthine et huile de lin épurée comme dissolvant
Sur
les ballons militaires français, le vernissage était généralement
appliqué à l'intérieur. On en passait 3 à 4 couches puis on finissait
avec un couche d'huile d'olive.
Sur
les ballons de petits volumes (jusqu'à 600 m3 environ) , on n'utilisait
qu'une couche d'étoffe que ce soit du coton ou de la soie. On renforçait
simplement aux endroits le nécessitant comme la collerette supérieure
autour de la soupape. On arrivait ainsi à des poids d'enveloppe proche
des tissus modernes du 21ième siècle.
Par
exemple, les ballons militaires français étaient fabriqués en soie
ponghée vernie qui pesait 237 gr/m². Les ateliers italiens Gavazzi de
Monza arrivaient, en utilisant de la soie italienne, à un poids de 160
gr/m² après vernissage.
Pour les ballons de volume plus importants, on multipliaient le nombre
de couches d'étoffes pour obtenir la résistance mécanique suffisante et
de fait on alourdissaient considérablement l'enveloppe.
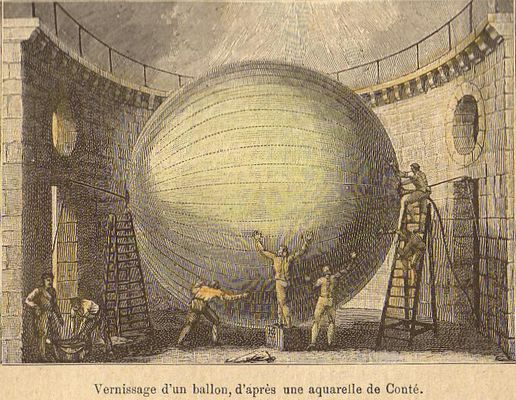
Cependant, ces opérations de vernissages étaient assez longues et très
dépendante de l'habileté des vernisseurs. De plus, avec le temps, le
vernis attaquait les étoffes leur faisant perdre résistance et
étanchéité. On s'est donc orienté vers les étoffes caoutchoutées.
–
Les étoffes
caoutchoutées
Ces
étoffes étaient généralement de couleur jaune à l'extérieur. Cette
teinture était à base de chromate de plomb ou d'aniline et servait à
protéger le caoutchouc des ultra-violets.
Sur
les étoffes vernies, les italiens utilisaient une teinture jaune
végétale appliquée sur l'étoffe avant vernissage.
●
L'étoffe simple
caoutchoutée
Utilisée pour de très petits volumes, on recouvrait uniquement l'une des
deux faces de l'étoffe. L'étanchéité n'était pas très bonne.
●
L'étoffe double
caoutchoutée,
Elle est composée de deux tissus de coton emprisonnant une pellicule de
caoutchouc et comportant une autre pellicule de caoutchouc sur une face
extérieure.
On
obtenait donc un sandwich avec un tissu jaune à l'extérieur du ballon,
une pellicule de caoutchouc, un autre tissu et une autre pellicule de
caoutchouc côté intérieur du ballon.
On
trouve plusieurs manières de disposer les deux tissus :
–
Deux tissus
identiques disposés parallèlement l'un sens trame l'autre sens chaîne
–
Deux tissus
identiques mais dont les fils trame et chaîne sont croisés à 45 °
Cette disposition a pour but de rendre la
propagation de la déchirure plus difficile par suite de
l'entrecroisement des fils. On la désigne sous le nom d'étoffe à fil
biais. Elle était utilisée sur les ballons de siège et sur les ballons
normaux à partir de 1910. On la trouve également sur les dirigeables
allemands et français.
–
Deux tissus
différents, celui à l'extérieur (donc apparent) est plus fin. Cette
étoffe a été peu utilisé car le tissu fin protégeait mal la pellicule de
caoutchouc intérieur.
Le
poids de ces étoffes se situaient aux environs de 300 à 400 gr/m²
Dans la deuxième moitié du 20ième siècle sont arrivés sur le marché des
matériaux synthétiques qui ont fait évolués ces étoffes.
Les caoutchoucs synthétiques :
Les
principaux utilisés dans l'aérostation sont le néoprène, l'hypalon et le
butyle permettent d'obtenir des propriétés intéressantes de résistance
aux éléments extérieurs et une bonne étanchéité.
●
Le Néoprène
Polychloroprene
commercialisé par DuPont de Nemours depuis 1931, Neoprene fut le premier
élastomère à usage spécial du marché. Ses propriétés particulières et
son excellent comportement en dynamique lui permettent de couvrir un bon
nombre d'applications dans de nombreux domaines. Véritable élastomère
pluridisciplinaire, Neoprene est un produit dont la renommée n'est plus
à faire.
Propriétés
- Echelle des
températures pour une utilisation normale : - 40°C+100°C
- Bonne résistance aux huiles et aux graisses pp
- Bonne résistance aux bases et acides minéraux dilués
- Bonne résistance à l'ozone, aux intempéries et à l'immersion dans
l'eau
- Excellente résistance aux flexions, torsion et à l'abrasion
- Bonne résistance à la flamme
- Faible déformation rémanente après compression
●
L'Hypalon :
C'est un caoutchouc synthétique (Polyéthylène
Chlorosulfoné ) largement utilisé dans les industries de
l'automobile, de l'électricité et du bâtiment en raison de ses
nombreuses propriétés remarquables et, notamment, de sa haute résistance
à l'ozone et aux intempéries.
Propriétés :
- Résistance aux intempéries et aux bactéries
- Insensibilité aux UV et à l'ozone
- Résistance à la température : - 40°C à +135°C (150°C en pointe)
- Résistance aux sollicitations mécaniques : usure, choc, abrasion
- Résistance aux agents oxydants tels que l'acide sulfurique et l'acide
nitrique, et aux produits chimiques corrosifs
- Bonne résistance à la flamme
- Résistance aux radiations nucléaires
●
Le butyl
Inventé en 1943.
Propriétés :
–
Grande résistance au
vieillissement
–
Inertie chimique
–
Très bonne
imperméabilité aux gaz, d'où son emploi dans les chambres à air de
pneumatiques
–
Faibles résistances aux
hydrocarbures.
Les tissus synthétiques :
Les principaux
utilisés sont le polyamide (Nylon) et le polyester. Ils ont permis un
allègement du poids tout en conservant une résistance suffisante.
Actuellement,
les étoffes utilisés pour les ballons à gaz sont composées de la manière
suivante :
–
Un tissu synthétique
tissé à 90°, généralement polyamide et parfois polyester (environ 65
gr/m²)
–
Une enduction intérieure
de plusieurs couches de butyl (environ 65 gr/m²)
–
Une enduction extérieure
de plusieurs couches d'Hypalon (environ 65 gr/m²)
Les tissus
utilisables pour gonfler à l'hydrogène doivent être antistatique. Pour cela, l'enduction de butyl est chargé de noir de carbone
ou graphite pour donner une conductivité suffisante au tissu.
C'est pourquoi
ces tissus ont généralement leur face interne noire sauf depuis peu ou
un constructeur allemand a développé une enduction conductrice blanche
pour éviter l'échauffement interne de l'enveloppe très pénalisant pour
les vols d'endurance.
Ce type de tissu
pèsent donc environ 200 gr/m² et une longévité d'environ 2 000 heures.
On peut
rencontrer des tissus, notamment aux USA, qui ont un tissu polyester ou
polyamide avec une enduction double face de polyuréthane.
Ils sont plus
léger (environ 140 gr/m²), l'étanchéité paraît bonne aux vues des
résultats en vols de longue durée mais nous n'avons pas d'informations
plus précises et notamment quant à la longévité de ce type d'étoffe. Ces tissus ne
sont pas antistatiques.
Une autre
paramètre très important qui n'a pas encore été abordé est ainsi celui
de la conductivité des tissus.
En effet,
depuis sa naissance, le ballon à gaz est gonflé principalement à
l'hydrogène. Les autres gaz utilisables sont le méthane, l'ammoniac et
l'hélium. Ces deux derniers ne sont pas inflammables donc les tissus
utilisables sont exempts de la nécessité d'avoir un tissu antistatique.
Ce problème
de conductivité apparaît déjà dans des ouvrages du début du 20ième
siècle ou des ballons ont été détruits lors du dégonflement alors que
les matériaux utilisés étaient naturels donc non générateur
d'électricité statique par frottement.
Explication
du problème :
●
Pourquoi
un ballon peut-il prendre feu ?
Pour
qu'il y ait feu, il faut trois paramètres :
–
un
carburant
–
un
comburant
–
une
énergie d'inflammation
Lors
qu'on vide un ballon, que ce soit par la soupape ou le panneau de
déchirure, il se crée par l'orifice de dégonflage, un mélange
air-hydrogène qui, si au même moment, est confronté à une source
d'inflammation, peut générer un incendie.
Ainsi,
si on peut se prémunir assez facilement des sources d'inflammation
telles que cigarettes ou flammes, la décharge d'électricité statique est
plus vicieuse. C'est elle qui est généralement la source des rares
incendies de ballon.
Pour
qu'il y ait étincelle, il faut une différence de potentiel électrique
entre deux éléments.
L'étincelle
due à l'électricité statique peut se produire entre :
–
un
éléments du ballon et le sol (le ballon se met « à la masse » ou « à la
terre »
–
un élément
du ballon et une personne s'approchant du ballon par exemple.
–
Deux
éléments du ballon chargés différemment.
●
Comment un
ballon se charge-t-il électrostatiquement ?
Le
ballon se charge de différentes manières:
–
Le
frottement de l'air sur les différents éléments du ballon lors des
mouvements ascendants et descendants générant une vitesse relative par
rapport à l'air environnant
–
Le
frottements des différents éléments entre eux (filet et tissu)
–
Le
frottement de l'hydrogène sur le tissu lorsque l'hydrogène est injecté
dans le ballon au gonflage et lorsqu'il est évacué par la soupape ou le
panneau
Au gonflage,
on peut considérer que les risques sont très limités car, si il n'y a
pas de fuite, il n'y a pas de mélange air-hydrogène qui se fasse.
L'hydrogène est directement injecté dans l'enveloppe vide d'air.
Au
dégonflage par contre, les risques sont plus grands. Le dégonflage au
panneau limite les risques car l'hydrogène est évacué très rapidement
(quelques secondes) et du côté opposé au sol (sur le dessus du ballon).
Dans les
divers ouvrages, nous n'avons pas encore trouvé le récit d'un incendie
après une ouverture au panneau de déchirure.
Lors d'un
dégonflage à la soupape (déconseillé par les constructeurs mais utilisé
par les pilote pour éviter d'avoir à recoudre la panneau de déchirure),
le risque est plus élevé :
–
Le temps
de dégonflage est augmenté (15 à 30 minutes)
–
Le pilote
vient enlever la soupape du ballon pour que l'hydrogène s'évacue plus
vite
–
L'orifice
de la soupape est proche du sol à la fin du dégonflement
Un autre
paramètre augmentant le risque est le temps. L'humidité augmente la
conductivité naturelle de tous corps. Ainsi, c'est par temps sec qu'il
faut être surtout vigilant.
●
Comment
sont conçus les matériaux pour éviter les étincelles d'électricité
statique ?
Des des
ouvrages du début du siècle derniers, ils avaient répondu à cette
question sans jamais la mettre en pratique. Il est vrai que les ballons
le nécessitait moins car entièrement en matériaux naturels.
Avec les
matériaux synthétiques qui génèrent beaucoup d'électricité statique, le
problème s'est vite posé durant les années 50.
La solution,
toujours utilisée aujourd'hui, est de rendre tous les éléments
conducteurs et surtout de les liés électriquement entre eux :
–
Les filets
sont tissés en incorporant un fil d'inox
–
La soupape
a tous ses éléments métalliques reliés entre eux par un fil métallique
–
Le tissu a
sa face interne conductrice
–
Tous les
éléments ont une liaison électrique entre eux
De cette
manière, le ballon est à l'équipotentiel c'est à dire que tous ses
éléments sont chargés du même potentiel électrique.
De plus,
lorsque la nacelle touche le sol, les suspentes de cette dernière
reliées elles aussi électriquement « déchargent » le ballon dès qu'il
touche le sol, bien avant que l'orifice de sortie du gaz ne s'approchent
du sol.
Pour
conclure, voler à l'hydrogène n'est pas plus dangereux que d'ouvrir sa
bouteille de gaz dans sa cuisine mais il y a des précautions à prendre :
–
utiliser
des matériaux conducteurs et reliés entre eux
–
dégonfler
le ballon au panneau de déchirure et pas à la soupape surtout lorsque le
temps est sec